Please note that some content is only available in Japanese
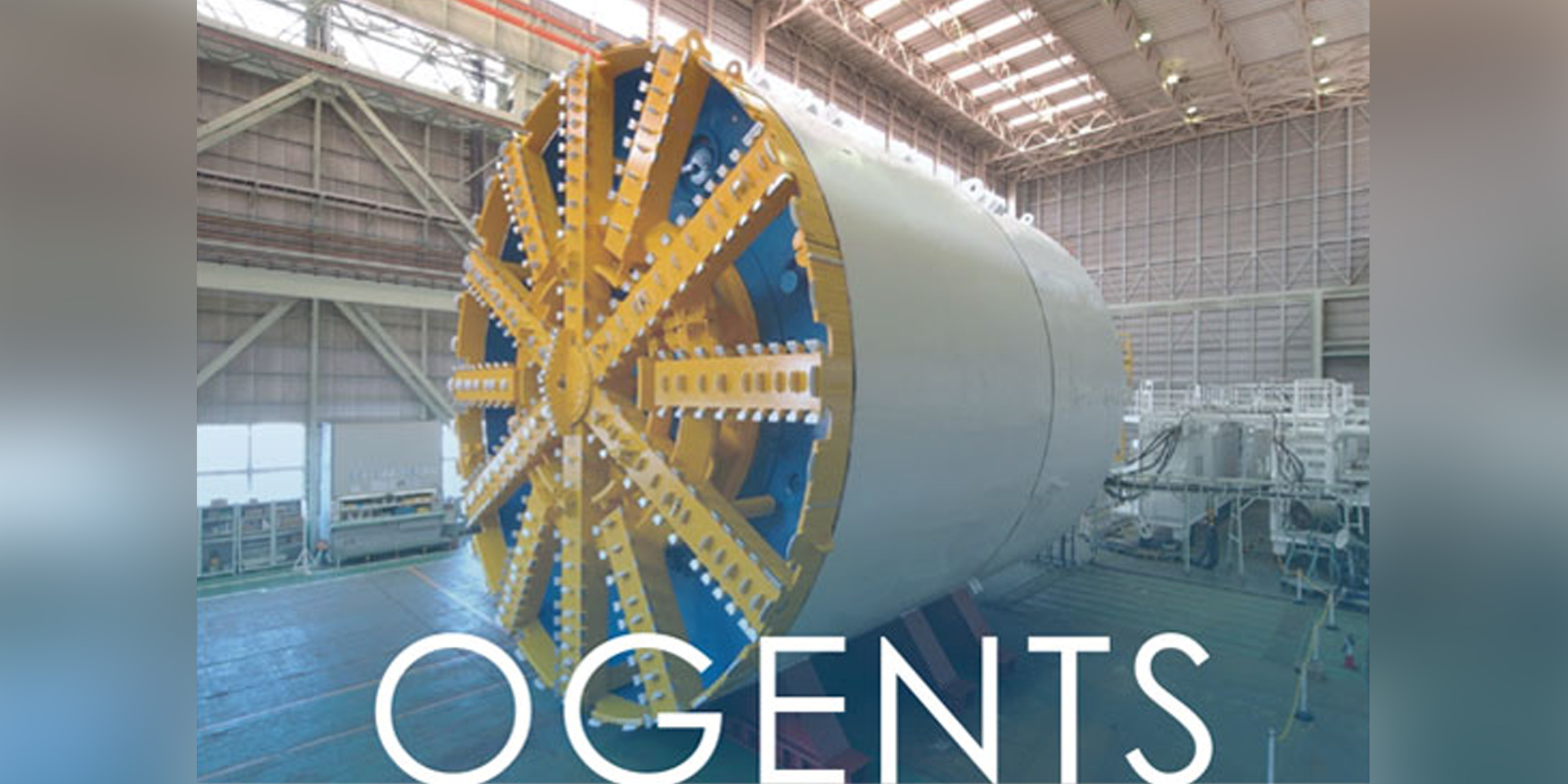
OGENTS
Automating various shield tunneling operations
POINT
-
Automating shield tunneling by integrating six types of work processes
OGENTS (Obayashi Intelligent Shield)
Among construction methods, shield tunneling is relatively advanced in terms of mechanization and automation; however, it still requires a large number of skilled workers. To address the growing labor shortage caused by population decline and aging, OGENTS integrates automation technologies for six key shield tunneling operations to achieve full automation of the entire process. This enables both labor savings and improved construction quality.
-
Six key shield tunneling operations
-
Labor-saving and efficiency improvements through automated surveying
OGENTS/SURVEY enables remote operation of a total station via a tablet device, eliminating the need for an assistant to reposition the prism—previously required for each measurement—allowing one person to complete the survey alone. The total station is equipped with an automatic prism detection and targeting function, and survey data is automatically transmitted, reducing work time by 30%.
Automating shield direction control with AI
OGENTS/DRIVE uses AI to control shield direction by selecting jacks based on learned operations from skilled operators. The AI automated driving has been applied at several sites, and its accuracy has been verified.
Unmanned operation through AI-driven automatic loading of excavated soil
Autonomous Backhoe Operation System
The Autonomous Backhoe Operation System uses data from measurement devices such as 3D LiDAR installed in the soil stockyard to allow AI to determine where to excavate and operate the backhoe automatically. The AI also identifies the location and weight of the soil to be loaded onto dump trucks.
Automatic control of backfill grout volume and pressure
Backfill grouting management interface
The “Automatic Backfill Grouting Management System” adjusts the volume and pressure of grout injection automatically, based on the excavation speed and size of the tail void. This ensures reliable backfilling and helps prevent surface and ground deformation.
Preventing equipment failure through preventive maintenance
Shield equipment integrated management screen
Data from each individual piece of equipment—monitored for operational health—is consolidated into a single interface. If signs of abnormality are detected, a warning is displayed.The Shield Equipment Integrated Management System is an automated inspection technology that collects operating data from each piece of equipment and detects signs of abnormalities to issue warnings. Preventive maintenance of shield equipment helps avoid potential failures before they occur.
Preventing accidents through unmanned segment transport and remote assembly
Segment Remote Assembly System
Segment transport from the surface stockyard to the tunnel face is automated, and segments are assembled via remote operation. This helps prevent accidents such as flying or falling objects and collisions during transport, as well as falls or entrapment during assembly.